سختیسنجی یکی دیگر از پارامترهای مهم در تولید چرخدنده فرآیند عملیات حرارتی میباشد که با این فرایند با توجه به محل کاربرد و نظر طراح به سختیهای مورد نیاز دست پیدا میکنیم و با توجه به روشهای مختلف عملیات حرارتی سختیهای متفاوتی در چرخدنده ایجاد میگردد به همین دلیل بایستی این پارامتر کنترل گردد. جهت کنترل سختی روشهای مختلفی وجود دارد که به اختصار شرح داده میشود.
روشهای اندازهگیری سختی
اساساً سختیسنجی در مقوله اندازهگیری فیزیکی جای میگیرد که در واحدهای صنعتی ما سختیسنجها در آزمایشگاههای اندازهگیری ابعادی به فراوانی مورد استفاده قرار میگیرند.
تعریف سختی چندان ساده نیست. بهعنوان معیاری از سختی، مقاومت به فرو رفتن شیء نافذ و بهعنوان معیاری دیگر، مقاومت در برابر خراشیده شدن را میتوان نام برد. همچنین لازم است به یاد داشته باشیم که سختیسنجی به دو روش استاتیکی و دینامیکی انجام میشود.
سختیسنجی استاتیکی
کلیات
بنا به تعریف، در سختیسنجی استاتیکی سختی مقدار مقاومتی است که ماده تحت آزمایش در برابر یک فرورونده از خود نشان میدهد. به این ترتیب، سختی با تغییر شکل ماده تحت آزمایش تحت اثر فرورونده متناسب است. این تغییر شکل در فلزات یا پلاستیکها دائمی، و در الاستومرها تغییر شکل الاستیک است. در اندازهگیری سختی مواد، میتوان به مقاومتهای کششی و فشاری، مقاومت در برابر ضربه و … که در نهایت تعیینکننده عمر قطعه مورد نظر است، نیز دست یافت. مثلاً استحکام کششی فولاد را با توجه به عدد سختی برینل آن میتوان با استفاده از روابط زیر بهدست آورد:
تجهیزات اندازهگیری سختی مواد:
اساس کار تجهیزاتی که امروزه در سختیسنجی مواد بهکار برده میشود، روش قیاسی است. به این معنی که ابتدا دستگاه با یک قطعه مرجع که اصطلاحاً به تکه آزمون معروف است، پیش تنظیم شده و سپس قطعات مورد تست با قطعه مرجع مقایسه میشود. نوک فرورونده معمولاً، به شکل کره (ساچمه) یا هرم بوده و مقدار سختی با نیروی وارده، شکل فرورونده و عمق اثر فرورونده متناسب است. به این ترتیب، میتوان گفت که اندازهگیری سختی بیشتر یک عیارگیری عملی است تا اندازهگیری عملی، زیرا نمیتوان مقداری مطلق برای سختی بهدست آورد.
روشهای سختیسنجی استاتیکی:
سختیسنجی به دو روش کلی در روی مواد انجام میگیرد: سختیسنجی به روش ماکرو و سختیسنجی به روش میکرو. در سختیسنجی به روش میکرو، تعیین سختی در حجمهای کوچک میکروسکوپی یک ماده امکانپذیر است، از این رو میتوان حتی سختی دانههای تشکیلدهنده یک ماده را بهطور مستقل و جداگانه نیز اندازهگیری کرد.
سختیسنجی به روش ماکرو، اندازهگیری مقدار تغییر شکل ماده مورد بررسی قرار گرفته و اندازه سختی براساس مقدار تغییر شکل مواد محاسبه میشود. در این بخش، تعدادی از روشهای سختیسنجی ماکرو توضیح داده میشود.
الف) سختیسنجی به روش برینل
در این روش با اعمال نیرو از طرف یک دستگاه هیدرولیکی به یک فرورونده که به شکل ساچمه فولادی است، عمل سختیسنجی انجام میگیرد. در اثر فشار از طرف گلوله فولادی به قطعه تحت آزمون، تغییر شکل پلاستیکی در آن قطعه ایجاد میشود. شکل حاصل از تغییر شکل پلاستیک بهصورت عرقچین بوده و با استفاده از قطر آن و قطر فرورونده طبق فرمول زیر عدد سختی به واحد برینل محاسبه میشود.
که در فرمول بالا:
P : نیروی اعمالی از طرف دستگاه به کیلوگرم نیرو
D : قطر فرورونده به میلیمتر
d : قطر عرقچین به میلیمتر
امروزه برای سهولت در عملیات اندازهگیری سختی به روش برینل، جداولی را طراحی کردهاند که بدون نیاز به استفاده از فرمول فوق، عدد سختی را مشخص میکند. برای این کار، نخست قطر عرقچین فرورفتگی را اندازهگیری و با درنظر گرفتن قطر فرورونده سختی مورد نظر را از جدول بهدست میآورند. اندازهگیری قطر عرقچین با خطکشیهایی که مجهز به یک دوربین با بزرگنمایی مشخصی است، انجام میگیرد. برای مثال یک دوربین با بزرگنمایی 20 دارای خطکشی با قدرت تمیز 005.0 میلیمتر است.
سختیسنجی به روش برینل محدودیتهایی دارد. در این روش لازم است دقت شود:
برای اجسام خیلی نرم یا خیلی سفت بکار برده نشود.
ضخامت جسم تحت آزمایش نباید کمتر از 5.2 میلیمتر و ترجیحاً کمتر از 5.6 میلیمتر باشد.
بهعنوان یک معیار عملیتر، ضخامت قطعه نباید کمتر از 10 برابر عمق نفوذ فرورونده باشد.
سختیسنجی باید حتیالامکان دور از لبههای قطعه انجام شود تا امکان قر شدن جانبی قطعه وجود نداشته باشد. با سنگ زدن یا پرداخت کردن سطح قطعه در محلی که قرار است فرورونده عمل کند، امکان بررسی دقیقتری از وضعیت گودی حاصل فراهم میشود.
لبه گودی وارده قابل تمیز نبوده و در برخی از مواد رنگین حتی مشاهده آن دشوار است.
![جدول 1- رابطه زمان بارگذاری با مشخصات مواد تحت آزمایش به روش برینل [6]](https://tgears.ir/wp-content/uploads/2023/03/table5-1.png)
ب) سختیسنجی به روش راکول
در این روش، اندازهگیری براساس عمق فرورونده محاسبه میشود. نوع شکل فرورونده دو نوع است. برای قطعات نرم از یک گلوله فولادی به قطر 5875.1 میلیمتر و برای قطعات سخت از یک مخروط با جنس الماسه با زاویه رأس استفاده میشود. در این روش اصول بارگذاری به فرورونده در دو مرحله انجام میگیرد. مرحله اول بارگذاری از 3 الی 10 کیلوگرم بوده، سپس بار ثانویه توسط اهرم دستی که قبل از اندازه بار آن تعیین شده است، اعمال میشود. عدد سختی به نوع کار فروروندهها را به 9 گروه طبقهبندی کردهاند که مهمترین آنها در جدول 5-2 داده شده است.
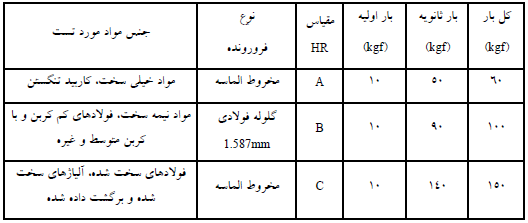
ج) سختیسنجی به روش ویکرز
از این روش برای قطعاتی که دارای سختی بالایی هستند از قبیل فولادهای کربوریزه شده یا نیتریده شده و … استفاده میشود. در این روش، شکل فرورونده، هرمی مربعالقاعده از جنس الماس بوده و زاویه بین دو وجه آن است. مقدار باری که در این روش سختیسنجی اعمال میشود متغیر و 1 تا 125 کیلوگرم نیرو بوده و عدد سختی به واحد ویکرز از رابطه زیر محاسبه میشود:
که در رابطه بالا:
P : نیروی اعمالی برحسب کیلوگرم نیرو
As : (میلیمتر مربع) سطح مقطع فرورفتگی
d : قطر اصلی فرورفتگی (میلیمتر)
α : زاویه تماس ایندنتور = 136 درجه
همچنان که در مورد سختیسنجی برینل گفته شد، جداولی از طرف سازنده دستگاه به خریدار عرضه میشود که او را از محاسبه بینیاز میکند. به این ترتیب کافی است وتر مربع فرورونده اندازهگیری و با مراجعه به جدول عدد سختی را به مقیاس ویکرز بهدست آورد.
د) سایر روشهای سختیسنجی ماکرو
روشها و مقیاسهای دیگری نیز برای اندازهگیری سختی وجود دارد. یکی از این روشها، روش اولتراسونیک است. اساس کار دستگاه سختیسنجی سونودور کاملاً متفاوت است. فرورونده در این دستگاه از یک نوک الماسی تشکیل میشود که به انتهای میلهای قرار دارد. میله با فرکانس ماورای صوت به ارتعاش درآمده و با نیروی 5.1 پوندی (حدود 8/8 کیلوگرم نیرو) با سطح قطعه تماس داده میشود. مقدار نفوذ فرورونده که با سختی قطعه متناسب است، بر فرکانس ارتعاش تأثیر گذاشته و آن را تغییر میدهد. مقدار تغییر بر روی نشاندهنده، پس از تبدیل به مقیاس راکول یا ویکرز بهطور الکترونیکی، قابل قرائت است.
این نوع سختیسنجها قابل حمل بوده و گودی بسیار کوچکی (کمی بیش از 01.0 میلیمتر) روی قطعه ایجاد میکند. بههمین دلیل، کاربرد آن در مواردی که حساسیت در این موارد وجود دارد مناسب خواهد بود. متأسفانه با این دستگاه فقط اندازهگیری سختی فولاد امکانپذیر است.
ه) سختیسنجی به روش میکرو
این روش سختیسنجی کاربرد وسیعی در اندازهگیری قطعات نازک و مواد میکروسکوپی دارد. دستگاههای میکروسختی از یک دستگاه سختیسنج و یک میکروسکوپ متالوژیکی تشکیل شده و دو نوع فرورونده در آن بهکار برده میشود. 1- هرم مربعالقاعده از جنس الماس که دارای زاویه بین وجوه متقابل آن بوده و از نوع فروروندههای ویکرزی است. 2- فرورونده نوپ که یک فرورونده هرمی کوچک از جنس الماس بوده و یک اثر هرمی را بر روی قطعه ایجاد میکند. نسبت قطرهای قاعده هرم برابر 7 به 1، زاویه بین وجوه مجاور در آن ، و و شکل حاصل از آن هرمی لوزی القاعده است.
عدد سختی در صورتی که از فرورونده مربعالقاعده (نوع اول) استفاده شده باشد، از رابطه زیر محاسبه میشود.
که در رابطه بالا:
F : بار اعمال شده برحسب گرم نیرو
d : قطر متوسط اثر قاعده هرم بر حسب میلیمتر
در صورتی که از فرورونده نوپ استفاده شده باشد، عدد سختی از رابطه زیر محاسبه میشود.
که در رابطه بالا:
F : بار اعمال شده برحسب گرم نیرو
d : قطر بزرگ قاعده اثر هرم لوزیالقاعده بر حسب میلیمتر
حداکثر بار اعمالی در روش میکروسختیسنج 400 گرم است.
و) تست سختیسنج پرتابل
اگرچه استفاده از تست راکول یا برینل بهصورت استاندارد و ثابت بهطور کلی ترجیح داده میشود اما همیشه امکان استفاده از این تجهیزات به علت شکل و محل قطعات وجود ندارد. در این مواقع تست سختیسنجی به کمک ابزارهای پرتابل بایستی صورت گیرد.
اندازهگیری سختی دینامیکی
کلیات:
سختی دینامیکی مواد با اندازهگیری میزان جهش یک جسم سخت پس از برخورد به سطح ماده تحت آزمایش بهدست میآید. هر قدر سختی فلز بیشتر باشد، ارتفاع جهش بیشتر خواهد بود. در اثر برخورد، اثر کوچکی روی قطعه کار باقی میماند، مقدار این اثر نشاندهنده پلاستیک قطعه مورد آزمایش است که نشاندهنده سختی استاتیکی فلز است. بخشی از انرژی پرتابه صرف ایجاد این اثر شده و تقریباً باقیمانده این انرژی صرف بازجهاندن پرتابه میشود.
انواع روشهای سختیسنجی دینامیکی:
از بین روشهای سختیسنجی دینامیکی تاکنون سه روش به مرحله کاربردی در جهان صنعت مطرح شده و مورد استفاده قرار گرفته است. سختیسنجهایی که بر اثر این روشها، ساخته شدهاند به این ترتیب هستند:
الف) اسکلرسکوپ
اولین نمونه این نوع سختیسنجها در سال 1907 توسط آلبرت اف.شر اختراع شد و به همین دلیل این نوع سختیسنجها را بیشتر بهنام سختیسنج شر میشناسند. سختی اسکلروسکوپ، سختی با واجهش یک «چکش» نوک هرمی که از ارتفاع معینی روی ماده تحت آزمایش سقوط میکند اندازهگیری میشود. از آنجا که در این روش، برجهندگی ماده مورد نظر اندازهگیری میشود، صیقلی بودن سطح آن بسیار اهمیت دارد.
ب) سختیسنج اکووتیپ
این روش یکی از جدیدترین و کارآمدترین روشهای سختیسنجی در صنعت است. واحد آن به افتخار مهندس دیتمار لیب، L یا L Value نامگذاری شده است. روش سختیسنجی اکووتیپ به این ترتیب است که یک گلوله از فولاد پارامغناطیس با نوک توپی شکل از جنس کاربید تنگستن به قطر 3 میلیمتر و به وزن 5/5 گرم تحت اثر نیروی یک فنر فشاری در داخل یک لوله از فولاد پارامغناطیسی پرتاب میشود. اگر سرعت گلوله در هنگام برخورد به سطح قطعه تحت تست که بستگی به نیروی فنر، جرم پرتابه و راستای حرکت پرتابه دارد V بنامیم و سرعت پرتابه پس از برخورد با سطح قطعه در زمان برگشت (در عکس جهت اصابت) v نامیده میشود، همواره V > v .
بدیهی است که تغییر شکل پلاستیک قطعه تحت آزمایش در محل برخورد باعث کاهش سرعت اولیه V میشود. انرژی جذب شده، به شکل یک فرورفتگی کوچک روی سطح کار قابل رویت است. از نظر تئوری، جسم مورد آزمایش اگر بینهایت سخت باشد . واضح است که چنین جسمی وجود خارجی ندارد. به هر حال، دو سرعت مذکور یعنی v و V تقریباً در یک میلیمتری نقطه برخورد گلوله با قطعه تحت آزمایش، اندازهگیری شده و ثبت میشود.
روش آشکارسازی به این ترتیب است که یک مغناطیس دائمی در بدنه گلوله قرار داده شده و عبور گلوله از داخل یک سیمپیچ جریانی را در سیمپیچ القا میکند. شار مغناطیسی با سرعت گلوله متناسب بوده و در نتیجه، جریان الکتریکی حاصل، ولتاژ بیشتری خواهد داشت. سیمپیچ در مکانی تعبیه شده است تا در یک میلیمتری نقطه برخورد، حداکثر میزان ولتاژ را داشته باشد.
پروب دستگاه که شامل پرتابگر و متعلقات آن است. بسیار کوچک و باریک بوده و اطلاعات آن از طریق یک کابل باریک به دستگاه پردازنده مرکزی منتقل میشود. اعداد بهدست آمده بلافاصله بهصورت دیجیتالی در مقیاسهای HRC، HB، HV، HRC و همچنین در مقیاس L بر صفحه نمایشگر ظاهر میشود. مجموعه این دستگاه قابل حمل بوده و قابلیت کار با باطری را نیز دارد.
یکی از قابلیتهای بسیار عالی سختیسنج اکووتیپ امکان استفاده آن در هر زاویه است. البته اطلاعات مربوط به زاویه در راستای حرکت گلوله میبایست قبلاً وارد دستگاه شود.
دیگر ویژگی این دستگاه دارا بودن پروبهای متفاوت است که محدودیتهای دستگاه را کم کرده و تواناییهای آن را افزایش میدهد. عدد لیب گستره بسیار وسیعی را معادل HV در برمیگیرد. یکی از مزیتهای روش سختیسنجی اکووتیپ نسبت به روشهای دیگر گستره اندازهگیری وسیع آن است. این دستگاه قادر است با استفاده از پروب بزرگتر، اندازه حرکت بیشتر، و در نتیجه انرژی برخورد بیشتری ایجاد کند که میتوان با کمک آن سختی قطعات ناصاف مانند قطعات ریخته و فورج را مستقیماً اندازهگیری کرد.
در جدیدترین دستگاه اکووتیپ قابلیتهای پردازش آماری و حافظهای نیز اضافه شده است. به همین دلیل، زمان و خطای اندازهگیری را بسیار کم کرده است. نقاط قوت دستگاه اکووتیپ عبارتند از:
- ظرفیت و کوچک بودن پروب
- سرعت بسیار بالا در انجام تست و خواندن نتیجه تست
- قدرت تفکیک بسیار عالی (900-200)
- خطای ناچیز در حد یا در حدود 6.0%
- قابلیت حملونقل آسان
- گستره وسیع همانند و معادل ویکرز
- تعمیر و نگهداری آسان
- دوام بالا
- عدم وابستگی به دما و زوایا
- موارد زیر نیز بهعنوان مزایای دیگری از این دستگاه قید شده است:
- صفحه نمایش بزرگ و واضح
- پردازش دادههای ریاضی و آماری
- قابلیت اتصال به پرینتر و کامپیوتر
لازم به یادآوری است که در تمامی مراحل ارزیابی سختیسنج اکووتیپ، نتیجه آن با سختیسنجهایی مانند شور[4] نیز قدم به قدم مقایسه شده است.
سختیسنج اکووتیپ عملکرد منحصر به فردی را در اندازهگیری سختی قطعات بزرگ و اجزای متوسط و ماشینآلات مختلف ارائه میدهد و از معدود سختیسنجهای قابل استفاده در این زمینه است. در عین حال، در ایستگاههای ثابت نیز بهخوبی وظیفه خود را انجام میدهد. برای استفاده در موارد مختلف از قبیل قطعات نازک، زبر و یا حجیم ملحقات متفاوتی به همراه سختیسنج اکووتیپ ارائه میشود که گاهی قیمت آن را تا دو برابر قیمت دستگاه اصلی بالا میبرد.
ج) سختیسنج کوپا
این دستگاه، یک سختیسنج دینامیکی بر پایه روش لیب است و به دلیل ویژگیهای برتر نسبت به سختیسنج اکووتیپ میتواند کاربردهای مفیدتری در صنعت داشته باشد.
این دستگاه همانند اکوتیپ از دو بخش پرتابگر و دستگاه مرکزی تشکیل شده است. این دو بخش توسط یک کابل به هم مرتبط هستند. بخش مرکزی این دستگاه تفاوت چندانی با اکووتیپ نداشته و در واقع یک رایانه ویژه با صفحه نمایش کریستال است. این دستگاه، قابلیت ارائه اطلاعات آماری و ذخیرهای لازم را دارد. همچنین دارای یک درگاه موازی است که به پرینتر و یا کامپیوتر میتواند متصل شود. این دستگاه مجهز به باطری قابل شارژ بوده و پرتابل است. اما بخش پرتابگر یا پروب این دستگاه تفاوتهای عمدهای نسبت به سختیسنج اکووتیپ دارد. در واقع تشابه آن با پرتابگر یا پروب اکووتیپ صرفاً در نوع گلوله است. به عبارت دیگر این گلوله نیز به وزن 5/5 گرم بوده و دارای نوک توپی شکل از جنس کاربید تنگستن و به قطر 3 میلیمتر است. در مقایسه با سختیسنج اکووتیپ، سختیسنج کوپا مزایایی دارد که به آنها اشاره میکنیم:
با سختیسنج کوپا حداکثر 5 برابر سریعتر از اکووتیپ میتوان عمل کرد. سختیسنج کوپا نیاز به شارژ دستی نداشته و پس از ضربه توسط خود دستگاه شارژ میشود.
انجام عملیات تست با کمک یک دست در سختیسنج کوپا بهراحتی میسر است. در حالیکه این عمل در سختیسنج اکووتیپ بسیار دشوار است.
نوک پروب پرتابگر کوپا باریکتر از نوک پرتابگرهای نرمال اکووتیپ است (16 میلیمتر در مقابل 20 و 25 میلیمتر). بنابراین انجام برخی تستها و اندازهگیریها که از زوایای باریک قطعه مورد آزمایش ضرورت مییابد با کمک سختیسنج کوپا امکانپذیر است.
سختیسنج کوپا تنها مجهز به یک پرتابگر کوچک است اما بهدلیل توانایی تغییر سرعت، قابلیتهای چند نوع پرتابگر اکووتیپ را یکجا ارائه میدهد. سختیسنج کوپا برای اکثر فلزات و سختیهای مختلف به تعویض پرتابگر نیازی ندارد.
بهعلت قابلیت کنترل سرعت گلوله در سختیسنج کوپا سرعت برخورد گلوله با قطعات مورد آزمایش در تمامی جهات یکسان است. در نتیجه دقت سختیسنج کوپا برای اندازهگیری سختی از زوایای مختلف یک قطعه با سطح خشن بیشتر از سختیسنج اکووتیپ برای چنین شرایطی است.
پرتابگر کوپا استهلاک بسیار کمتری نسبت به پرتابگر اکووتیپ دارد زیرا بهجای استفاده از ماشه مکانیکی، از کلید الکتریکی و بهجای استفاده از نیروی مغناطیسی آهنربای دائم (که تقریباً در معرض ضربه قرار میگیرد) از حسگرهای نوری و بالاخره بهجای استفاده از نیروی فنر از نیروی الکترومغناطیسی سود میبرد که نتیجتاً استهلاک و هزینههای تعمیر و نگهداری آن کمتر از سختیسنج اکووتیپ است.
استهلاک گلوله کوپا بسیار کمتر از گلوله اکووتیپ است، زیرا برای هربار آزمایش با دستگاه اکووتیپ، گلوله آن چندبار با سطح قطعه مورد آزمایش برخورد میکند (معمولاً بیش از ده بار برخورد مشاهده میشود) و در حالیکه گلوله کوپا برای هر بار تست فقط یک بار با سطح جسم مورد آزمایش برخورد دارد. همچنین تعداد ضربات در گلوله اکووتیپ سبب تضعیف آهنربای دائم که در آن تعبیه شده است میشود و در نتیجه موجبات اختلال در سیستم اندازهگیری را فراهم میآورد.
بنابراین عوامل مذکور یعنی تعداد ضربات گلوله در هر بار تست، و وجود آهنربای دائم در داخل گلوله اکووتیپ مجموعاً سبب میشوند که گلوله اکووتیپ که بسیار حساس و گرانقیمت است عمر کمتری داشته باشد. بهطوری که براساس دفترچه راهنمای اکووتیپ، گلوله پس از 3000 بار تست باید تعویض شود. در صورتیکه این عدد برای سختیسنج کوپا به بیش از 100000 بار میرسد.
از آنجا که اساس کار دستگاه اکووتیپ بر پدیده میدان الکترومغناطیسی استوار است، این دستگاه برای سختیسنجی در مکانهایی که دارای میدان مغناطیسی بالاتر از 4 گوس هستند مجاز نیست. این محدودیت در سختیسنج کوپا وجود ندارد زیرا اصولاً مکانیزم کار آن متفاوت بوده و اندازهگیری سرعت گلوله با حسگرهای نوری انجام میپذیرد.
نوک توپی شکل گلوله در سختیسنج کوپا حدود 5.0 میلیمتر از پوزه بیرون میزند و به همین علت اندازهگیری سختی اجسامی با سطوح نسبتاً ناهموار با سختیسنج کوپا میسر است. در حالیکه نوک گلوله اکووتیپ حدود 1.0 میلیمتر از پوزه بیرون میآید و این زائده کوچک در اندازهگیری سطوح ناهموار محدودیت ایجاد میکند.
عدد سختی را در نقشههای فنی بهصورت مقادیر حداقل و حداکثر (مثلاً HRC45-50) یا بهصورت تلرانسی (BHN 300±30) نشان میدهند. در برخی موارد، محل اندازهگیری سختی روی نقشه قطعه مشخص میشود زیرا امکان تغییرات مقدار سختی در نقاط مختلف آن وجود دارد. بنابراین مهم است که اندازهگیری سختی در نقطه تعیین شده انجام شود.
بدون نظر