برای اینکه چرخدندههای مخروطی بدون سروصدا داشته باشیم باید دارای فاصله دندانه یکنواخت، دندانههای هم مرکز با محور دوران و شکل دندانههای یکسان باشند. بیدقتی در هر کدام از پارامترهای فوق باعث سروصدا خواهد شد. علاوه بر آن شکل پروفیل و تصحیحات انجام شده روی آن در میزان خطای نسبت تبدیل و سروصدا بسیار مؤثر است. برای بررسی موارد فوق از ماشینهای تست چرخدندههای مخروطی استفاده مینماییم.
آزمون درگیری
یکی از دستگاههای معمول برای آزمون چرخدندههای مخروطی، دستگاه تست درگیری میباشد در این دستگاه جفت چرخدنده در موقعیت صحیح نصب میشوند و با یک بار ترمزی چرخدندهها را میچرخانیم.
نرمی و سروصدای درگیری، اثر تماس دندانهها، اندازه دندانهها، کیفیت پرداخت سطح، لنگی چرخدنده و خطاهای فاصله بین دو دندانه در این آزمون کنترل میشود. این آزمونها در دو مرحله قبل و بعد از عملیات حرارتی انجام میشود.
الگوی تماس
الگوی تماس معرف صحت شکل دندانه در راستای پروفیل و در راستای طولی آن میباشد. اثر تماس دندانهها با چند ثانیه درگیری آنها و به کمک رنگ تهیه میشود.
ماشین آزمون
ماشینهای آزمون چرخدندههای مخروطی دارای تنظیم محوری برای هر دو عضو کرانویل و پینیون میباشد و تنظیم عمودی خروج از مرکزی برای کم یا زیاد نمودن فاصله بین محورهای دو عضو در حین آزمون برای چرخدندههای هیپوئیدی استفاده میشود.
تنظیم محوری پینیون برای بررسی اثر تغییرات زاویه فشار روی الگوی تماس مورد استفاده قرار میگیرد و تنظیم محوری کرانویل بهمنظور کنترل لقی جانبی و تنظیم خروج از مرکزی عمودی محورها بهمنظور بررسی اثر زاویه مارپیچ روی اثر تماس مورد استفاده قرار میگیرند.
علاوه بر آن به کمک این تنظیمات، میتوان تغییرات لازم برای تنظیمات ماشین را بهمنظور تغییر موقعیت و مشخصات الگوی تماس بهدست آورد.
کنترل پروفیل دندانه که در مورد چرخدندههای ساده و مارپیچ استوانهای مرسوم است به دو دلیل برای چرخدندههای مخروطی انجام نمیشود. اول اینکه، شکل دندانههای مخروطی در هر موقعیت، از ابتدا تا انتهای دندانه تغییر میکند این در حالی است که شکل دندانه در چرخدندههای ساده از ابتدا تا انتها یکسان است بنابراین اطلاعات متفاوتی در کنترل دندانه از ابتدا تا انتها بهدست میآید. دلیل دوم اینکه، حتی اگر این کنترل بهصورت عملی قابل انجام باشد تماس صحیح دندانه را در طول کامل دندانه مانند ماشینهای آزمون نمیتواند نشان داد.
در دستگاههای آزمون چرخدندههای مخروطی به منظور نصب صحیح چرخدندهها، از فیکسچرهای خاصی استفاده میشود که برای جفت چرخدندههایی با مشخصات متفاوت تغییر میکند و باید مجدداً طراحی شود.
نحوه انجام آزمایش
وقتی که جفت چرخدنده مخروطی با نسبت تبدیل جدید تولید میشود در ابتدا لازم است که جفت چرخدنده بهینه شود. یعنی اینکه موقعیت و شکل الگوی تماس در محل مناسبی قرار گیرد و از نرمی و کم سروصدایی جفت چرخدنده در شرایط کاری نهایی اطمینان حاصل شود. این مسأله قبل از تولید انبوه چرخدندهها صورت میگیرد.
در ابتدا تنظیمات برای تولید پینیون و کرانویل محاسبه میشود و پس از تولید اولین جفت چرخدنده، آنها با یکدیگر روی ماشین آزمون کنترل میشود تا میزان تغییرات لازم برای تنظیمات دستگاه پینیون بهدست آید. این تغییرات بهمنظور درنظر گرفتن اعوجاجهای عملیات حرارتی و تغییرشکلهای نصب صورت میگیرد.
معمولاً تمامی تغییرات روی پینیون صورت میگیرد زیرا تغییرات مشخصات پینیون بسیار سریعتر و رضایتبخشتر میباشد. پس از بهدست آوردن میزان تغییرات از روی ماشین آزمون و اعمال آن روی ماشین دندهزنی پینیون، مجدداً پینیون تولید میشود و با کرانویل در دستگاه آزمون درگیر مینمایند و کنترل میشوند. این فرآیند تا بهبود کامل مشخصات چرخدندههای درگیر صورت میگیرد و پس از بهدست آوردن تنظیمات صحیح، تولید انبوه صورت میگیرد.
به منظور تکرارپذیری تولید پس از رسیدن به مشخصات نهایی، چندمجموعه چرخدنده دقیق با نام چرخدنده کنترل تولید میشوند تا با چرخدندههای تولیدی روی ماشین آزمون درگیر شوند و مشخصات آنها بررسی میگردد.
دستگاههای آزمون
دو نوع دستگاه آزمون چرخدندههای مخروطی موجود میباشد یکی با زاویه 90 درجه و دیگری با زاویه قابل تنظیم که در شکلهای (1) و (2) نشان داده شدهاند.
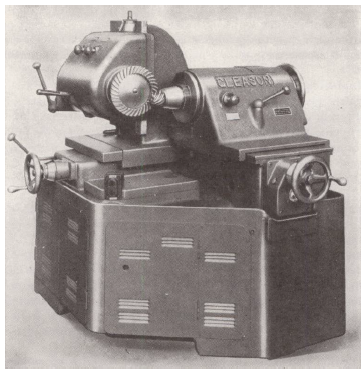

نحوه آزمون و بهبود
در حین بهبود سه عامل باید مدنظر باشد:
1- جفت دنده باید نرم و آرام درگیر شوند بهعبارتی سروصدای درگیری آنها کم باشد.
2- باید تنظیمات لازم بهمنظور جلوگیری از تمرکز بار روی لبههای دندانه صورت گیرد.
3- اندازه، شکل و موقعیت الگوی تماس باید مطابق کاربرد چرخدنده باشد.
بهمنظور درگیری آرام چرخدندهها، الگوی تماس باید دارای مساحت زیاد باشد. این عامل باعث افزایش پایداری سطح در مقابل سایش نیز خواهد شد ولی با افزایش مساحت الگوی تماس، قابلیت تنطیم چرخدنده کاهش مییابد. به همین دلیل باید بین نرمی درگیری و قابلیت تنظیم، تعادلی برقرار شود و بدین ترتیب الگوی بهینه تماس بهدست آید.
درنظر گرفتن تغییرات عملیات حرارتی و تغییر شکلهای نصب
دندانهها پس از عملیات حرارتی دچار تغییرات کمی خواهد شد. میزان این تغییرات به اندازه و شکل چرخدنده و روش عملیات حرارتی بستگی دارد. علاوه بر آن تغییر شکلهای تکیهگاههای محل نصب چرخدندهها در اثر بار، باعث میشود که چرخدنده در محل نصب تئوری خود قرار نگیرد و مشخصات الگوی تماس تغییر کند. این تغییرات تا اندازهای در دستگاههای آزمون قابل شبیهسازی هستند.
آزمون عمودی و افقی بودن
آزمون افقی و عمودی بودن روشی برای اندازهگیری میزان و جهت تغییر مکانهای عمودی و محوری پینیون از موقعیت استاندارد آن بهمنظور فراهم نمودن الگوی تماسی در میانه دندانه و در انتهای کوچک و انتهای بزرگ دندانه میباشد.
معمولاً الگوی تماس در بار سبک، باید مساوی نصف طول دندانه باشد. دلیل این امر آن است که امکان جبران تغییر شکلهای نصب و قابلیت تنظیم کافی وجود داشته باشد. برطبق مطالب بیان شده، آزمون عمودی و افقی بودن بهترین و دقیقترین روش طول الگوی تماس میباشد.
با توجه به مطالب بیان شده، روش آزمون چرخدندههای مخروطی سخت، زمانبر و گران میباشد و پیشبینی و اصلاح اعوجاجهای عملیات حرارتی نیز سخت میباشد. در آزمونهای عملی بیان شده با چند بار سعی و خطا و تکرار آزمایشها، خطاهای پروفیل دندانه اصلاح میشوند و بهعلت خطاهای سیستماتیک دستگاه، پسزنی ابزار و اعوجاجهای حرارتی و … تنظیمات واقعی چرخدنده تولیدی مشخص نمیباشد و بهصورت تئوری نمیتوان الگوی تماس را بررسی و تحلیل نمود.
چند اشکال عمده در آزمونهای عملی چرخدندهها وجود دارد نخست اینکه، آزمایشها بسیار وابسته به اپراتور است و افراد متفاوت ممکن است نتایج متفاوتی را از یک جفت چرخدنده بهدست آورند. دوم اینکه، این روش کنترل مقدار کمی برای خطاها بهدست نمیدهد. سوم اینکه با آزمون، مشخص نمیشود که خطا مربوط به کدام یک از جفت دندانه درگیر میباشد.
با استفاده از روش اندازهگیری پروفیل دندانه میتوان خطاهای بیان شده را در زمان بسیار کمتری اصلاح نمود و تنظیمات چرخدنده واقعی را بهدست آورد. علاوه بر آن میتوان تنظیمات یک چرخدنده تولیدی ناشناخته را بهدست آورد که در طراحی معکوس چرخدندهها بسیار مفید است.
بدون نظر