از آنجا که ماشینکاری، روشی متداول برای تولید چرندندههای مخروطی میباشد، مقاله حاضر بر آن است که فرآیند مهندسی معکوس جهت طراحی قالب فورج دقیق برای تولید چرخدنده مخروطی دیفرانسیل تراکتور را تشریح کند. این فرآیند با بررسی نقشههای خارجی موجود از قطعه، ترسیم در محیط نرمافزاری CAD، تهیه نقشهای اجرایی از قالب مراحل پیش فرم و الکترودهای اسپارک آغاز شده، با تحلیل فرآیند در نرمافزار Super Forge ادامه مییابد. از طرف دیگر با توجه به تولید چرخدنده با روش فورج دقیق بسیاری از عواملی که در فورج معمولی از آن صرفنظر میشود باید در فورج دقیق لحاظ گردد، از این رو به بررسی تأثیر عواملی نظیر ضرایب اصلاح قالب، روانکاری، مقدار اکسیداسیون و تغییرات دمایی در اثر انتقال حرارت و نیز اصطکاک قطعه با دیواره قالب در طراحی قالب نیز پرداخته شده است. در پایان نمونههای واقعی ساخته شده با نتایج تحلیلی نرمافزار مقایسه گردیده و انطباق خوبی را در زمینه فرآیند تولید و نیروی مورد نیاز شکلدهی نشان میدهد.
کلید واژگان: چرخدنده مخروطی، فورج دقیق، تولید به حالت شکل نهایی[1] و نهایی[2]، مدلسازی سهبعدی، CAD/CAM
1- مقدمه
فرآیند فورج دقیق در اکثر کشورهای جهان بهعنوان روشی رایج جهت تولید انواع قطعات فورج از جمله چرخدندههای مخروطی بهکار میرود که هدف از این فرآیند تولید قطعات بدون پلیسه یا با حداقل پلیسه است. بهعبارتی در مقایسه با روش ماشینکاری سنتی، این روش باعث افزایش تیراژ تولید قطعات، کاهش زمان ماشینکاری و اتلاف مواد میگردد. از طرفی امروزه کابرد سیستمهای CAD/CAM در روشهای گوناگون ساختوتولید باعث تسریع فرآیند طراحی و تولید قطعه گردیده است.
فرآیند فورج نیز بهعنوان یک روش شکلدهی حجمی اولین بار بعد از جنگ جهانی دوم در کشور آلمان غربی پایهگذاری شد بهطوری که این کشور از ترکیب سیستمهای CAD/CAM و روشهای طراحی قالب فورج دقیق برای اولین بار موفق به تولید چرخدنده مخروطی کامین شدند. امروزه تعداد چرخدندههای مخروطی ساخته شده با فورج دقیق به حدود 17 میلیون عدد در سال میرسد که بیش از 70% کل تعداد چرخدندههای تولیدی را در بر میگیرد.
2- فرآیند فورج دقیق
فرآیند فورج دقیق یا فورج با تلرانس بسته در دو حالت فورج گرم و سرد انجام میگیرد. مهمترین مزیت فورج دقیق حذف یا کاهش حجم اتلاف مواد و صرفهجویی در هزینه ماشینکاری است، زیرا با توجه به تحقیقات انجام گرفته حدود 40% از وزن یک قطعه با فورج معمولی تبدیل به پلیسه میشود، از طرفی خواص مکانیکی قطعات فورج دقیق بالاتر از قطعاتی است که بعد از فورج معمولی ماشینکاری میشوند و این بهعلت عدم آسیب به نحوه جریان مواد بعد از انجام فورج میباشد.
فرآیند فورج دقیق برای چرخدهندهها بهصورت فورج گرم انجام میشود که هر دو مزیت تنش تسلیم پایینتر نسبت به فورج سرد و دقت بالاتر نسبت به فورج داغ را دارا میباشد. فرآیند فورج دقیق تابع پارامترهایی است که در ذیل به توضیح مختصر آنها میپردازیم:
2-1- درجه حرارت فرآیند
مهمترین عامل مؤثر در فرآیند فورج دقیق درجه حرارت فرآیند میباشد. حرارت بالا باعث کاهش دقت ابعادی و ایجاد اکسید در سطح قطعه میشود و از طرفی به دلیل ایجاد تنشهای حرارتی باعث کاهش عمر قالب میشود، اما با این وجود دما هرچه بالاتر باشد سیلان مواد داخل قالب راحتتر بوده و نیروی فورج کاهش مییابد. با توجه به تحقیقات انجام شده برای فولادهای آلیاژی و کربنی دمای بین 750 تا 850 درجه سانتیگراد بهترین دماست. با توجه به اینکه در فورج دقیق حرارت از طریق تشتشع و هدایت انتقال مییابد گرمای حاصل در قطعه بهصورت میباشد که TI دمای اولیه قطعه، TD دمای تولید شده در اثر تغییر فرم پلاستیک، Tf افزایش دما در اثر اصطکاک و Tt کاهش حرارت در اثر انتقال میباشد. حرارت تولید شده ناشی از تغییر فرم پلاستیکی قطعه بهصورت زیر است که در آن σa تنش سیلان قطعه، εa کرنش متوسط، A ضریب تبدیل انرژی مکانیکی به حرارتی، ρ وزن مخصوص قطعه و C گرمای ویژه قطعه کار و B ضریبی از تغییرشکل (معادل 95%) میباشد.
و گرمای تولید شده در اثر اصطکاک:
که در آن f ضریب اصطکاک که M از جدول شکلدهی بهدست میآید، V سرعت بین مواد و قالب در فصل مشترک، F مساحت ناحیه تماس قطعه و Va حجمی از قطعه کار است که در معرض افزایش دما قرار دارد.
انتقال حرارت از طریق قالب
که در آن h ضخامت مواد بین نیمه قالب و TP درجه حرارت سطح قالب است.
2-2- جنس قالب
بهعلت اینکه فولاد بهکار رفته در فرآیند فورج دقیق باید مقاوم به سایش بوده و سختی آن حدود 60-55 (HRC) باشد. لذا فولادهای گرم کار با افزودن 5% کروم و ایجاد سطح نیتریده سختی لازم جهت فرآیند فورج را بهدست میآورند. در این مقاله جنس قالب H11 درنظر گرفته شده است.
2-3- روانکارها
2-4- دقت قطعه پیش فرم
از آنجا که فورج دقیق چرخدنده مخروطی در چندمرحله انجام میگیرد افزایش دقت قطعه پیش فرم روی کاهش مقدار دورریز مواد، سیلان مواد و نیز پرشدن قالب تأثیر خواهد داشت لذا هرگونه کمبود حجم مواد بیلت یا پیش فرم باعث پر نشدن حفره قالب و زیادتر بودن مواد آنها نسبت به حالت معمولی، باعث افزایش اعمال فشار به قالب و دستگاه میشود.
2-5- اصلاحات ابعادی روی الکترود اسپارک
با توجه به اینکه قالبها در روش فورج دقیق به روش اسپارک تولید میشوند پارامترهای زیر روی ساخت الکترود باید اعمال گردد.
- همواره مقداری گشادی کناری حین اسپارک کاری که تابعی از آمپراژ، جنس الکترود و ولتاژ دستگاه میباشد ایجاد میگردد که از راه تجربی محاسبه شده و الکترود باید به آن مقدار کوچکتر شود.
- الکترود اسپارک به مقدار انبساط حرارتی قالبها در اثر پیش گرم کردن باید کوچکتر شود.
- از آنجا که دمای قطعه خروجی از قالب نهایی بیشتر از دمای محیط بوده و تا رسیدن به دمای محیط مقداری منقض میشود لذا الکترود اسپارک به مقدار این تغییر بعد باید بزرگتر گردد.
3- محاسبات چرخدنده مخروطی جهت ترسیم در نرمافزار Solidworks
مهمترین جزء در طراحی چرخدندهها و ترسیم مدل آنها بهدست آوردن پروفیل دندانه میباشد، که در تمام چرخدندهها از دو حالت اینولوتی و یا حالت سیکلوئیدی تبعیت میکند. در چرخدندههای مخروطی با توجه به اینکه در طول پهنای دندانه از سمت انتها به سمت پیشانی چرخدنده مقطع دندانه کوچکتر میشود، لذا یک چرخدنده مخروطی در هر مقطع از عرض دندانه دارای مدول متفاوت است ولی در تمام محاسبات از مدول ماکزیمم استفاده میشود. بههمین جهت میتوان منطبق کردن پروفیل بزرگ دندانه چرخدنده مخروطی در قسمت انتهایی بر دندانه چرخدنده ساده معادل، چرخدنده سادهای را با پارامترهای مشابه بهدست آورد که از آن جهت تعیین مختصات نقاط منحنی اینولوتی بهره جست. شکل 1 را ببینید.
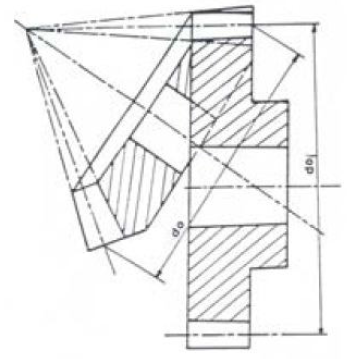
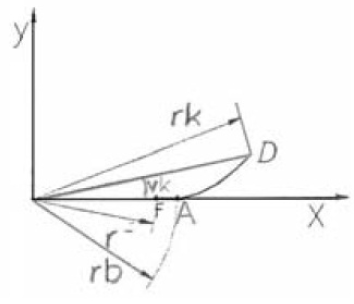
با استفاده از همین قانون از معادلات چرخدنده ساده معادل برای طراحی چرخدنده مخروطی بهصورت زیر استفاده شده است البته لازم به ذکر است که روی نقشه نمونه خارجی این قطعه مقادیر ارتفاع سر دندانه h، ارتفاع ته دندانه hf، زاویه فشار (α)، زاویه رأس مخروط (d) و دیامترال دندانه و نیز تعداد دندانهها مشخص شده است. سایر ابعاد چرخدنده جهت تولید شکل سهبعدی آن نیز در نرمافزار Solidworks نظیر ارتفاع کل چرخدنده، قطر سوراخ چرخدنده توسط کولیس اندازهگیری شده و اندازهگیری فیلتها هم از طریق شابلونهای فیلت ویژه انجام گرفته است. فرمولهای چرخدنده ساده معادل بهصورت زیر میباشد:
که در آن drk قطر دایره سردنده، dvb قطر دایره اصلی و Zr تعداد دندانههای معادل میباشد و بعد از محاسبه مقادیر فوق مرحله ترسیم پروفیل اینولوت دنده آغاز میشود. سپس باتوجه به پارامترهای مربوطه کار طراحی در محیط CAD انجام میگیرد.
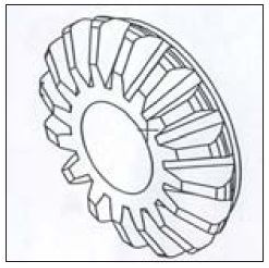
4- جنس قطعه کار
مواد اولیه قطعه چرخدنده از جنس فولاد کربنی کروم و منگنزدار با گرید 27MC5 JV ذکر شده است. فولاد مورد نظر در استاندارد S53 1112 به دو قسمت 27MC5 و JV تقسیم شده است که قسمت اول در استاندارد B53 1344 بهطور کامل تفسیر شده است و قسمت دوم به مفهوم پیروی از مقادیر سختی جامینی است که نتایج تست جامینی مذکور نیز در استاندارد B53 1344 قید شده است. ترکیب شیمیایی ذکر شده برای این فولاد در استاندارد بهصورت زیر میباشد.
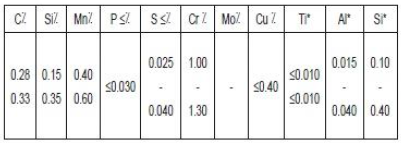
با توجه به استاندارد معرفی شده در نقشه شرکت گوادونی، برای تولید این قطعه فولاد 27MC5 JV معرفی شده است. در کلید فولاد گرید مشابهی برای این فولاد با استاندارد فرانسوی AFNOR وجود ندارد. در نقشههای قطعات دیگر دیفرانسیل و گیربکس مثل کرانویل و … برای این فولاد، فولادهای جایگزین 27CD4 و 23MCD5 معرفی شده است. با توجه به مطالعات و بررسی تمامی فولادهای سمانته با آنالیز نزدیک به فولاد موردنظر جدول 2 تهیه شده است.
همانطور که در جدول نشان داده شده، فولاد 7131.1 از لحاظ آنالیز نسبت به سایر فولادها مشابهت بیشتری با فولاد مورد نظر دارد و هم اینکه در بازار داخلی یافت میشود.
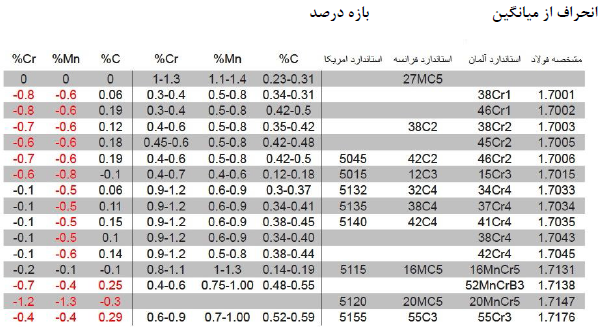
5- تعیین پارمترهای فورج
بعد از انجام طراحی قطعه در محیط نرمافزار Solidworks با اعمال چگالی قطعه در داخل نرمافزار میتوان حجم و جرم قطعه ماشینکاری شده را بهدست آورد. برای طراحی قطعه نهایی فورج تغییراتی شامل اضافه مواد ماشینکاری (که با توجه به جدول مربوطه این مقدار تعیین و به سطح پیشانی و پشتی چرخدنده مخروطی افزوده میشود)، تعیین سطح جدایش (در مورد سطح جدایش این سطح باید بهگونهای انتخاب شود که از دندانههای چرخدنده مخروط که باید بهصورت نهایی و یا نزدیک به حالت نهایی تولید شود عبور نکند، لذا در این حالت سطح جدایش چرخدنده را بهصورت خط شکسته درنظر میگیریم شکل 4 نحوه تعیین خط جدایش را نشان میدهد)، طراحی راهگاه، اعمال شیب به دیواره خصوصاً دیواره سوراخ مرکزی چرخدنده که به راهگاه منتهی میشود (این برای جلوگیری از چسبیدن قطعه به قالب است) و در نهایت فیلت در قطعه اعمال میشود.
برای تعیین پارامترهای فورج که در بالا اشاره شده از استاندارد DIN7523 استفاده گردیده است. بدین ترتیب مقدار جرم و سطح و حجم قطعه فورج نهایی در نرمافزار Solidworks تعیین شده و طراحی مراحل فورج آغاز میگردد. با توجه به نکات ذکر شده در مطالب قبل برای فورج چرخدنده مخروطی مطابق با منابع مختلف سه مرحله درنظر گرفته میشود که شامل مراحل زیر است:
1- مرحله اول شامل عملیات کلهزنی[3] با اپست
2- مرحله دوم شامل عملیات فورج با قالب بسته که در آن قطعه سوراخداری ایجاد میشود که این سوراخ در قالب فورج نهایی با معکوس قرار دادن قطعه مرحله دوم بهعنوان راهنما عمل کرده و به کاربر در قرار دادن صحیح قطعه داخل قالب کمک میکند.
3- عملیات فورج با قالب بسته نهایی که در آن قطعه نهایی با مقطع شکل 5 تولید میشود.
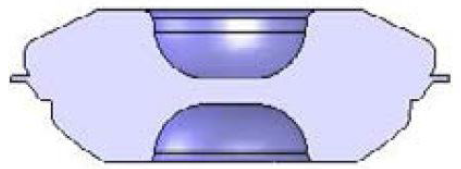
برای طراحی قطعات پیش فرم و بیلت اولیه از قانون برابری جرم و حجم استفاده میشود، از طرفی مقداری اضافه مواد برای هر مرحله جهت درنظر گرفتن مقدار اکسیداسیون سطح قطعات در مراحل مختلف درنظر گرفته شده است.
6- تعیین ضرایب اصلاح و طراحی نهایی قالب و الکترود اسپارک برای هر مرحله
بعد از انجام طراحی قسمتهای مختلف قطعات پیش فرم و بیلت باید ضرایب اصلاح قطعات برای طراحی قالب و الکترود اسپارک محاسبه شود. برای این کار ابتدا باید مقدار تنش سیلان کل فرآیند و نیز کرنش کل را محاسبه کرد وجود این مقادیر بعداً در بهدست آوردن مقدار دما و قطعه بر اثر تغییر شکل پلاستیک در قالب نهایی TD و نیز افزایش دما در اثر اصطکاک در قالب Tf مورد نیاز خواهد بود، از طرفی دمای قطعه موقع خروج از قالب نهایی بهصورت T است که مقدار TI 800℃ فرض شده، یعنی قطعه موقع استقرار در قالب نهایی باید دارای دمای 800℃ باشد. برای محاسبه تنش سیلان مواد در کل فرآیند ابتدا مقدار کرنش واقعی و نرخ کرنش در هر مرحله محاسبه و سپس با استفاده از فرمول تنش سیلان در هر مرحله بهدست میآید. در این رابطه K تنش تسلیم فولاد 4130 در دمای 800℃، n توان کرنش سختی، m ضریبی است که مقدار آن از جدول مربوط استخراج میشود، ε کرنش برای هر مرحله از شکلدهی است که عبارت است از مجموع کرنشهای واقعی اعمال شده به قطعه در هر مرحله و مراحل شکلدهی قبل از آن و å نرخ کرنش در هر مرحله شکلدهی است و از رابطه حاصل میشود. در این رابطه v سرعت حرکت پرس میباشد که از جدول 3 استخراج میشود و h نیز متوسط تغییرات ارتفاعی بین دو مرحله میباشد. با اجرای این روش برای هر سه مرحله فورج مقدار کل کرنش و تنش سیلان محاسبه میگردد.
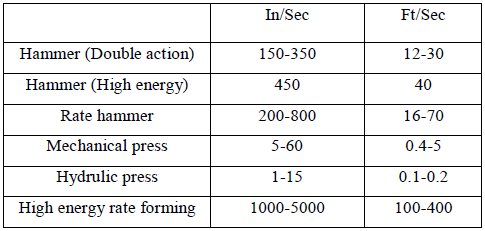
برای محاسبه ضریب انقباض قطعه بعد از خروج از قالب نهایی ضخامت دندانه بهعنوان مبنا فرض میشود و تغییرات این بعد بهعنوان ضریب بر قطعه فورج نهایی اعمال میشود. ضرایب اصلاح پیش گرم قالب و ضریب اصلاح گشادی کناری اسپارک نیز دو ضریب دیگر هستند که در مورد قطعه فورج نهایی محاسبه و بر آن اعمال میشوند. در مورد قطعه پیش فرم مرحله میانی نیز فقط دو ضریب اصلاح پیش گرم قالب و اصلاح گشادی کناری اسپارک تأثیر داده میشود. البته لازم به ذکر است که با توجه به تحقیقات انجام شده در این پروژه مقدار گشادی کناری ایجاد شده توسط الکترود اسپارک از هر طرف 2/0 میلیمتر درنظر گرفته شده است.
7-محاسبه دمایی که بیلت در آن دما از کوره باید خارج شود
از آنجایی که دمای قطعه پیش فرم دوم موقع استقرار در قالب نهایی 800℃ درجه سانتیگراد درنظر گرفته شده و از طرفی در طول مراحل پیش فرم اول و دوم در اثر تماس قطعه با قالب دمای قطعه کار کاهش مییابد (مقداری از حرارت هم بهصورت همرفت در حین جابجایی قطعه بین قالبها تلف میگردد) لذا این پارامتر نیز باید در طراحی قطعه در فرآیند فورج دقیق تأثیر داده شود.
در این رابطه مقادیر اتلاف گرما بهصورت همرفت هنگام انتقال بین قالبها از رابطه بهدست میآید که ℃T=800 دمای قطعه موقع استقرار در قالب نهایی، TO دمای قطعه موقع خروج از قالب و 20℃ –∞T دمای محیط میباشد، مقدار m نیز از رابطه که A سطح جسم، V حجم کلی جسم، h ضریب همرفتی، ρ دانسیته جسم و C ظرفیت گرمایی ویژه بهدست میآید. از طرفی جهت محاسبه کاهش دما قطعه کار در تماس با دیوارههای قالب از فرمول استفاده میشود که TD دمای پیش گرم کردن قالبها، t زمان فرمدهی پرس، T1 دمای قطعه کار موقع قرار گرفتن در قالبها، TO دمای قطعه کار در هنگام خروج از قالب است که در مرحله قبل توسط فرمول همرفتی محاسبه شده است m’ نیز ضریبی است که مقدار آن از رابطه حاصل میگردد که در آن R ضریب انتقال گرمای تماسی میباشد و از جدول مربوطه محاسبه میشود. مقدار زمان فرمدهی t توسط جدول 4 بیان میشود. با توجه به محاسبات انجام شده طبق روش بالا بیلت باید تا دمای حرارت داده شود قالبها نیز در حالت فورج بسته تا دمای 200℃ پیش گرم میشوند. از طرفی در فورج چرخدندههای مخروطی بهتر است بیلت استوانهای باشد بر همین مبنا ابعاد بیلت در این مقاله با ارتفاع 68/43 میلیمتر و قطر آن 5/37 میلیمتر درنظر گرفته شده است.
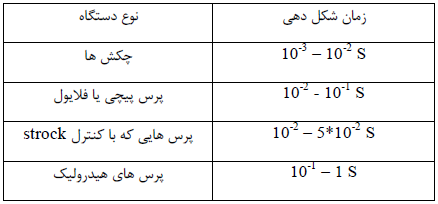
8- شبیهسازی فرآیند توسط نرمافزار SF[4]
امروزه با پیشرفتهای انجام شده در جهت شبیهسازی فرآیندهای شکلدهی طراح میتواند قبل از انجام واقعی فرآیند مقدار نیرو، عیوب احتمالی و تنشهای احتمالی وارده بر قطعه و قالب را رویت کرده و در صورت نیاز آنها را تصحیح کند. نرمافزار SF یکی از این نرمافزارهاست که ورودی آن قطعات با فرمت STL (شبکهبندی مثلثی) میباشد و کار شبیهسازی فرآیندهایی نظیر رولینگ، فورج، خمکاری و اکستروژن را انجام میدهد. بهطور کلی برای انجام فرآیند فورج در نرمافزار SF پارامترهای زیر باید به نرمافزار معرفی شود:
8-1- جنس قالب و قطعه
جنس مواد را میتوان از کتابخانه خود نرمافزار انتخاب کرد یا در صورت نیاز و عدم وجود جنس مزبور پارامترهای آن را تعریف و به نرمافزار معرفی کرد.
8-2- نوع پرس
برحسب فرآیند مورد نظر میتوان انواع چکش و پرسهای لنگ، هیدرولیکی، پیچی و … را به نرمافزار معرفی کرد.
8-3- اصطکاک
8-4- دمای قطعه و قالب
9- مراحل انجام شبیهسازی نرمافزار
در انجام فرآیند تحلیل در این مقاله تمامی پارامترها به دقت تعریف شده البته وجود تجارب قبلی در زمینه آهنگری صنعتی میتواند کاربر را در استفاده از این نرمافزار به مقدار زیادی یاری دهد. بعد از تعریف این پارامترها عملیات مماس کرددن قالب بالا و پایین به قطعهای که باید فورج شود انجام میگیرد و سپس پارامترهای شکلدهی نظیر تعیین طول کورس پرس، اندازه المان جهت تحلیل (هرچه این مقدار کوچکتر باشد دقت تحلیل بالاتر ولی زمان آن نیز بیشتر خواهد بود)، و در نهایت نوع فرآیند که بهصورت آهنگری قالب بسته یا باز است باید تعریف شود. مراحل انجام تحلیل چرخدنده مخروطی دیفرانسیل تراکتور کمرشکن باغی در این مقاله به شرح زیر است:
9-1- مرحله کلهزنی
در این مرحله که بهصورت فورج با قالب باز میباشد از پرس مکانیکی استفاده شده، و مقدار ضریب اصطکاک 25/0 میباشد. مقادیر دمای قطعه و قالب نیز با توجه به محاسبات انجام شده در بخشهای قبلی بهصورت متناوب به نرمافزار اعمال میشود. دمای بیلت در این مرحله هنگام ورود به قالب 85/832 سیلسیوس میباشد. بعد از انجام فرآیند ورود بیلت و قالبهای فورج باز به محیط نرمافزار SF و انجام فرآیند ران کردن، قطعه حاصل از این مرحله بهصورت شکل 6 تولید شده است. در این مرحله ارتفاع بیلت از مقدار 68/43 میلیمتر به مقدار 28 میلیمتر کاهش یافته، در نمودار 1 نیروی لازم برای فرآیند کلهزنی نیز نمایش داده شده است.
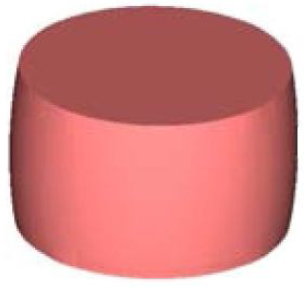
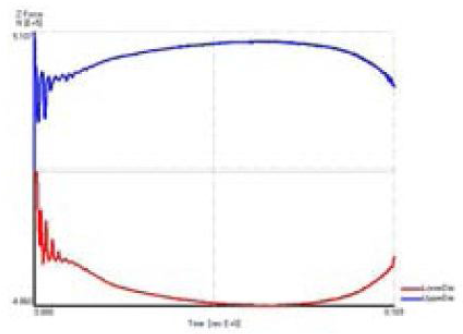
9-2- مرحله میانی
در این بخش که بهصورت فورج با قالب بسته انجام میگیرد، حجم قطعه کاملاً با حجم قالب بعد از بسته شدن برابر بوده و پلیسهای در ضمن این مرحله تولید نخواهد شد. این مرحله توسط یک پرس هیدرولیکی انجام میگیرد و مقدار ضریب اصطکاک نیز 25/0 فرض شده است. در این مرحله قطعه اپست شده مرحله اول به همراه قالبهای مدل شده در نرمافزار SW با فرمت STL وارد محیط نرمافزار SF شده و فرآیند تحلیل بهصورت متوالی انجام میگیرد. قطعه تولید شده در این مرحله (شکل 7) قطعه ورودی برای قالب فورج نهایی است، نمودار نیروی لازم جهت انجام فرآیند نیز در شکل زیر نشان داده شده است.
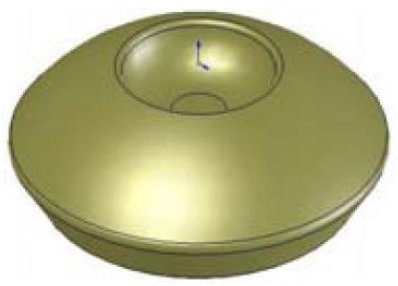
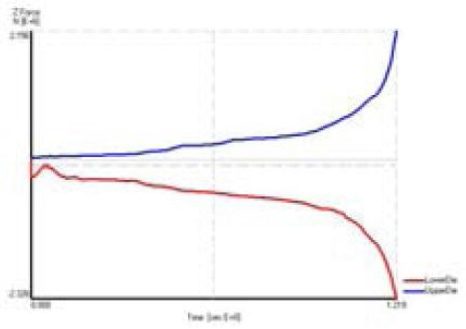
مرحله فورج نهایی
در این مرحله چرخدنده بهصورت شکل نهایی با پلیسه تعیین شده، تولید میشود. در آغاز، قطعه مرحله میانی بهعنوان قطعه ورودی مرحله نهایی به این بخش مشخص میشود از طرفی مدل قالبهای نیز از نرمافزار SW با پسوند STL به نرمافزار SF منتقل میشوند. میزان ضریب اصطکاک نیز 25/0 درنظر گرفته شده است.
از طرفی برای این مرحله هم که بهصورت فورج با قالب بسته انجام میگیرد از پرس هیدرولیکی استفاده گردیده است. در شکل زیر قطعه نهایی و نمودار نیروی فورج مرحله نهایی نشان داده شده است.
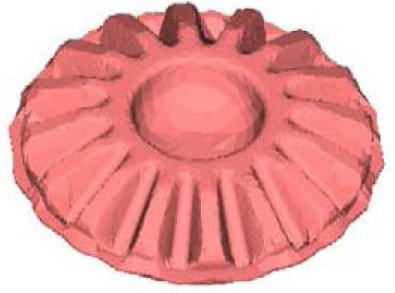
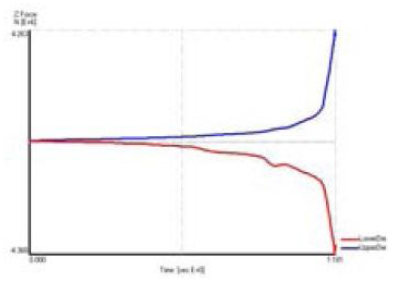
جهت رویت عیوب در بخش نهایی تولید، به دلیل حساسیت قطعه تولیدی تعداد فریمهایی که در آن میتوان شکلدهی چرخدنده را رویت کرد افزایش داده شده است. در پایان این فرآیند نیز قالب و قطعه را در چند جهت برش زده و مقاطع از لحاظ نحوه پر شدن و عدم ایجاد عیوب مورد بررسی قرار میگیرند.
10- تعیین منحنی نیرو-کورس بهصورت گام به گام
در این بخش سعی شده تا نمودار نیرو-طول کورس فورج قالب نهایی بهصورت مرحله به مرحله از نقطه شروع تا نقطه انتهایی بهدست آید. از آنجا که زمان کل شکلگیری چرخدنده، در قالب فورج نهایی با شرایط تعریف شده (شامل تعیین نوع پرس، میزان اصطکاک، جنس مواد و قالب و دمای قطعه و قالب) حدود 181/1 ثانیه و طول کورس از محل مماسی قالبها بر قطعه 12 میلیمتر حاصل شده است لذا نتایج شبیهسازی در فواصل 20%، 40%، 60%، 80%، 90%، 100% از طول کورس تولید بررسی گردیده است. در ضمن شکلهای زیر گامهای شکلگیری قطعه نهایی در درصدهای ذکر شده از فرآیند فورج را نشان میدهد.
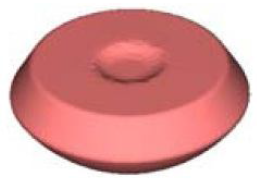
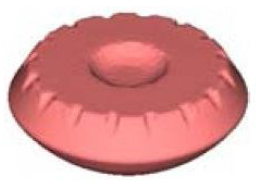
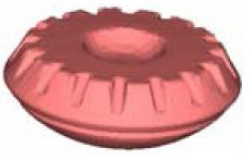
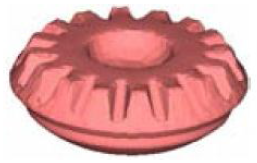
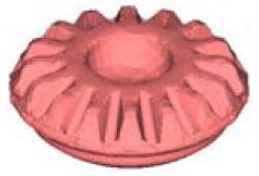
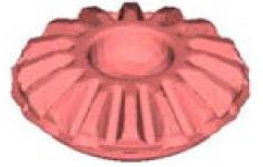
به همین ترتیب میتوان نمودار مربوط به هر بخش از انجام فرآیند را بهدست آورد. با مشاهده تصاویر بالا میتوان دریافت که در مرحله 20% اولین قسمت قالب بالایی که با قطعه درگیر میشود نافی قالب بالا است که برای ایجاد سوراخ مرکزی چرخدنده مورد استفاده است، بهعبارتی در این قسمت هنوز دندانههای قالب با قطعه درگیر نشده است. مقدار نیرو جهت شکلدهی با استفاده از رسم منحنی در هر بخش قابل دسترسی است. در رسم منحنیهای زیر مقادیر X طول کورس برحسب متر و مقادیر Y نیروی F برحسب نیوتن میباشد. در مرحله 40% اولین درگیریهای قالب بالا جهت شکلدهی دندانهها انجام میشود. با توجه به نمودارهای طول کورس-نیرو مشاهده میشود با کاهش طول کورس نیروی فورج جهت پر کردن تمام زوایا و گوشههای قالب افزایش مییابد.
منحنی حالت 100% در بیشترین مقدار خود، تناژ پرس مورد نیاز جهت عملیات فورج و منحنی هر مرحله نیز ماکزیمم مقدار نیرو (تناژ پرس) برای انجام آن مرحله را نشان میدهد. مقادیر عددی برای رسم هر نمودار متوسط خود نرمافزار SF تولید و رسم منحنیها نیز در محیط Excel انجام گرفته است.
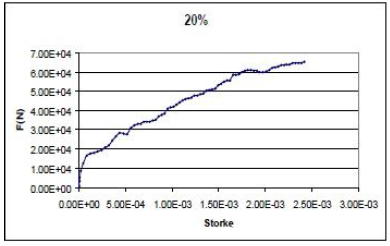
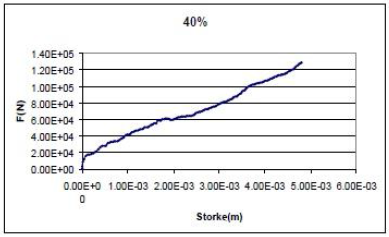
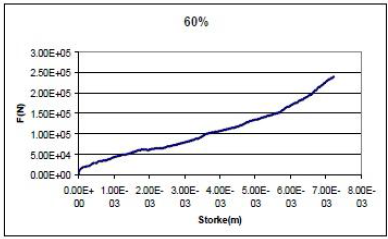
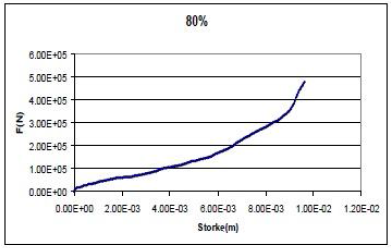
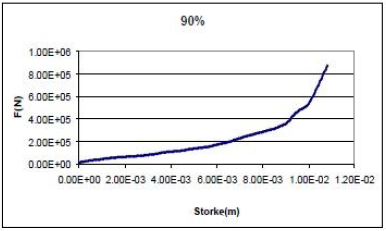
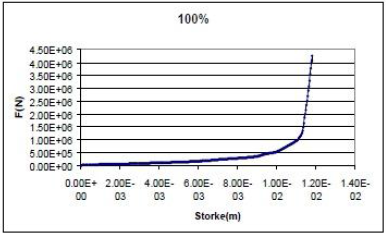
از طرف دیگر با استفاده از امکانات نرمافزار SF میتوان مقادیر تنش، کرنش، دما و … را بهصورت نموگرام رنگی برای هر نقطه از قطعه ایجاد کرد که محدوده هر رنگ مقدار تنش، کرنش، دما یا … را در آن نقطه نشان میدهد. بهطور مثال شکل 15 مقدار تنش در قطعه فورج با استفاده از نموگرام رنگی را نشان میدهد.
11- تعیین نیروی مورد نیاز فورج چرخدنده
با توجه به تحلیل فرآیند و نمودارهای نیرو-زمان ذکر شده در نرمافزار مقادیر زیر برای هر مرحله از فورج چرخدنده هرزگرد تعیین شد:
فورج باز، فورج با قالب میانی، فورج با قالب نهایی
برای اطمینان از صحت ادعای نرمافزار با استفاده از نمودار تجربی استاندارد DIN مقادیر نیرو برای هر مرحله با این روش نیز بهدست آمد:
فورج باز، فورج با قالب میانی، فورج با قالب نهایی
که مقادیر درصد خطا از فورج باز به سمت فورج با قالب نهایی نسبت به نمودار تجربی بهترتیب 10%، 4.6% و 7.6% بوده است. با توجه به اینکه نیروی فورج در مرحله سوم بیشترین مقدار است لذا مقدار نیروی لازم برای پرس حدود 160 تن معرفی گردید. لازم به ذکر است که در عمل نیز کار فورج قطعه و قالبها با پرس 160 تن انجام گردیده است.
12- نتیجهگیری
با توجه به اینکه ماشینکاری روش سنتی تولید چرخدندههای مخروطی میباشد که به نوبه خود پرهزینه و زمانبر است، چرخدنده مخروطی به روش فورج دقیق طراحی و بهینهسازی شده و نتایج زیر از مقاله قابل حصول میباشد.
1- تولید چرخدنده مخروطی به روش فورج دقیق باعث افزایش تیراژ تولید، کاهش زمان ماشینکاری و اتلاف مواد میگردد.
2- استفاده از نرمافزارهای CAD کار تولید مدل سهبعدی و تهیه نقشههای اجرایی و نیز تلرانسگذاری نقشهها، تصحیح خطاها و … را تسریع میکند.
3- با استفاده از نرمافزار تحلیلی SF میتوان فرآیند فورج را بهینهسازی و شبیهسازی کرده و مقادیر نیرو، کرنش، تنش، تغییرات دما و حتی دیاگرام نیرو-طول کورس و … را بهدست آورد.
4- با توجه به نمودارهای رسم شده برای نیرو-طول کورس میتوان مقادیر نیرو در هر بخش از فرآیند فورج و تناژ نهایی پرس را برای انجام آن مرحله بهدست آورد.
5- نمونههای ساخته شده با نتایج تحلیلی نرمافزار از لحاظ عیوب رویت شده در قطعه در حین فورج و نیروی مورد نیاز انجام فرآیند مقایسه گردیده و انطباق خوبی میان نتایج حاصل از هر دو روش بهدست آمده است.
مراجع:
[1] Doege, E., Weber, F., “Economical manufacturing of gear by near net shape”; Forging proc. of 29 Matador,PP. 421, 1992.
[2] Stickels, C., Samanta, S.K., “Cold forging in gear manufacturing”; Metals Eng. Quarterly, PP. 59, 1974.
[3] Meges, W., “Application of new forming process in gear and drive manufacture”; VDI Berichte, No 332, pp. 97, 1979.
[4] Badaway, A., Altan, T., “Application of CAD/CAM techniques to close tolerance forging of spiral bevel gears”; Annuals of CIRP, PP. 141, Vol31, 1981.
[5] Tomove, B.I., Gagor, V.I., “Modelling and description of the near net shape forging of cylinderical spur gear”; J. Materials processing technology; pp. 92-93, 1999.
[6] Maitra, G.M., “Hand book of gear design”; 1990.
[7] DIN7523 (German Standard), “Steel forging”,1989.
[8] Lange, K., “Hand book of metal forming”; Published by society of manufacturing engineers (SME), 1985.
[9] DIN7526 (German Standard), “Steel forging tolerances and permissible uariations for drop-forging”; 1969.
10- سایت مجلات فنی و مهندسی ساخت و تولید www.irmpm.com
IRAN MANUFACTURING & PRODUCTION MAGAZINE
[1] Near-net-shape
[2] Net-shape
[3] uppsetting
[4] Super Forge
بدون نظر